Graphite Machining Techniques -
As far as machine arrangement, the one significant tip to recollect is to consistently try not to utilize coolant. Graphite is a genuinely permeable material, thus it can ingest coolant and go about as a "coolant wipe," which will cause issues with finished parts. Inside the machine and on the tooling, the coolant can really respond with the graphite dust and make a grating slurry, which will cause issues while machining. A vacuum framework or dust collector is suggested for clearing material while machining graphite. Any other way, covered apparatuses ought to have the option to run dry.
Something else to note while machining graphite is that since graphite doesn't deliver chips, but rather a haze of extremely grating dust, it tends to be destructive to operators and machines without legitimate consideration. Operators ought to be wearing a protective mask to try not to breathe in the graphite dust. Appropriate ventilation and keeping up with air quality in the shop is likewise key for the security of engineers when working in graphite.
Since the graphite dust is likewise incredibly conductive, it can undoubtedly harm non-defensive circuits inside your CNC machine, which can cause major electrical issues. While coolant isn't suggested, a vacuum framework can assist in removing the dust, holding it back from aggregating a lot inside the machine and preventing major issues.
We are focused on giving quality parts at serious costs when you need them.
Methods for Graphite Machining
Graphite machining can be done using the following five methods:
- Compression molding
- Isostatic molding
- Vibration molding
- Die molding
- Extrusion
All five of these methods make use of fine graphite powder made from either natural or synthetic graphite.
Unique Characteristics for Machined Graphite -
1. Density
Dense graphites are used to machine parts where geometry is critical. However, material removal is often better with less dense graphite.
2. Grain Size
With very fine grain graphites, the wear decreases and the surface finish improves. On the other hand, material removal is less, block sizes decrease, and prices increase.
3. Electrical Resistivity
The lower the electrical resistivity, the higher the thermal conductivity. Therefore, the graphite has the ability to dissipate the energy accumulated during each discharge. Thus, the wear rate decreases with electrical resistivity.
4. Flexural Strength
The higher the flexural strength, the easier the fine detailed machining and the lower the wear.
5. Hardness
The higher the graphite hardness, the more difficult it is to machine the electrode.
6. Settings
Graphite used in negative polarity gives a faster machining speed than positive polarity with a wear rate of about 20% regardless of the intensity level. However, machining in positive polarity leads to wear rates approximately 10% to 50% in finish mode (with a current intensity less than 5A) and about 0% in roughing mode (current intensity greater than 25A), while diminishing the risk of abnormal discharges, as previously mentioned.
In practice, the operator will normally use graphite in positive polarity when in roughing mode, except for straight through holes where the wear is not a critical factor. Machining in finish mode will be accomplished in negative or positive polarity dependent upon the stability of the process. To obtain process stability, it is advisable to work with smaller current densities in negative polarity (45 A/in2) than in positive polarity (60 A/in2).
Equipment used in Graphite Machine
Using CNC equipment that can reach more than 20,000 rpm is significant for effectiveness. Eventually this is identified with the measure of material that is eliminated with every turn of the tooling. You would essentially prefer not to move the machine quicker at a similar rpm. All things considered, you can raise the rpm, and in keeping the feed per upset something very similar, you raise the feed pace of the machine. All tools have ideal feeds and velocities, however this is a significant idea for graphite processing.
The CNC equipment ought to likewise be fitted with a clearing framework to secure moving surfaces inside the machine. At the point when graphite is cut, it transforms into a grating powder. Utilizing a clearing framework keeps within the machine and the region around the machine as spotless as could be expected. Allowing the graphite dust to get into orientation or bearing surfaces on a CNC machine is asking for a disaster.
Graphite Machining Products
EDM Electrodes -
Our Clients
World-renowned companies like Devu tools, Dietech India, MothersonSumi Systems, Kangaro, Seco Warwick, and many others have entrusted us in supplying their Graphite needs. And now it’s your turn to take the benefits of our quality services!
1200+
Clients
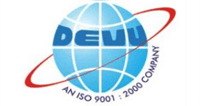
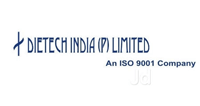
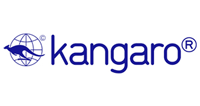
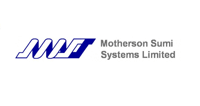
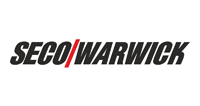